.
TechTalk
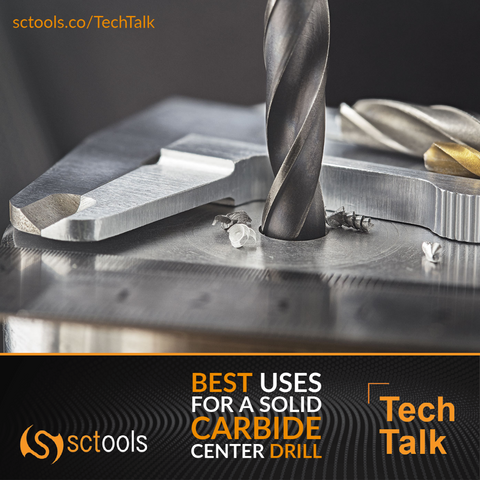
Best Uses for a Solid Carbide Center Drill
Drills are essential tools in any kit. No matter what industry you're in, you will need drills that can cut holes in plastic, metal, or a combination of all three - all while adhering to strict quality and measurement standards.
If the drill bits you use are not up to the task, even the highest quality drill won't be of much use. In the end, drill bits determine your drill's overall capabilities.
The higher price of carbide center drills is justifiable on a cost-per-part basis because of its ability to produce large holes. These tools usually have internal coolant ducts to ensure higher tool life and steady production for deep high-volume holes.
The carbide center drill can cut centering holes on shaft faces held between two centers while performing other CNC tasks.
It is very beneficial to use solid carbide drills for exceptional hole quality, process security, and manufacturing economy. The best performance comes from the combination of penetration rate and precision, with accuracy that exceeds IT8. You can also increase your cost efficiency by reconditioning your solid carbide drills.
Different Kinds of Carbide Drills Bits or Inserts
-
Carbide Drill Bits or Inserts
Carbon (Carb) drill bits are the hardest and brittlest drill bits out there. This drill's design makes it perfect for production drilling using high-quality tool holders and equipment. Carbide drills bit are not suitable for hand drills or drill presses.
With the ability to handle the most challenging materials, these drill bits deliver an exceptional drilling performance. To drill through metal, you must use a drill bit that can withstand heat.
To get the best results on your project, look for a bit made to handle the type of metal you're working with, and that makes a clean, precise hole. For hard surfaces, masonry bits with carbide or durum tips are more efficient and penetrate the surface faster and more profound.
Tungsten carbide drill bits are typically made of tungsten carbide, although they may vary in composition from small amounts of cobalt or zinc to reduce their reactivity with iron. Carbide drill bits usually come in one of two forms, carbide-tipped or full-body.
Manufacturers produce drill bits using an alloy of steel; they are often reinforced or made more
rust-resistant by coating them with another material, as described below.
-
High-speed steel (HSS)
Due to its affordability and ability to cut through wood, plastic, and soft steel. The name "HSS drill bits" refers to the fact that they cut faster than other types of steel.
Even though manufactures can use high-speed steel for most maintenance tools, it is less suitable for industrial tasks.
-
Cobalt
Cobalt drill bits consist of a steel alloy containing 5-8% cobalt to cut steel and solid metals such as cast iron.
-
Titanium
Usually, Titanium drill bits are made from steel and coated in titanium, so they aren't as durable
or strong as cobalt drill bits, and they may lose the coating over time.
Center Drill Bits
In metalworking, center drill bits can create a starting hole for a larger-size drill bit. Many manufacturers refer to center drill bits as Slocombe drill bits or self-centering drill bits. The drill bit cannot move in a peripheral direction on the workpiece once hole-forming has begun.
When mounting a lathe center on a workpiece, Slocombe drill bits are also used to indent conical holes in a workpiece and are available in different sizes and sets. Their tips consist of two pieces: the small pilot and the sizeable countersinking area. The cost of center drills varies from spot drills to center drills.
Plain-tipped Cobalt Steel Center Drills
In the high-speed machining of hard materials, cobalt steel center drills are more rigid and provide good wear resistance when compared to high-speed steel center drills. Plain-tip center drills are the most common choice for preparing stock for turning between centers by creating center holes in it.
Plain-tipped Extended Length Center Drills
Center drills extended in length have a longer working area than standard center drills and offer more accessible access to hard-to-reach workpieces. The plain tip of these center drills is the most
the standard tip used to drill center holes into stock to be turned between centers on a lathe.
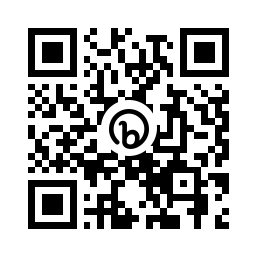
If you have any questions about carbide cutting tools or taps, be sure to reach out to us @ sctools.co/Home or call us at (877)737-0987. We help you machine better!
Comments (0)